Bell Tuning
Tuning a bell is a process we approach with precision and the careful skill of our most experienced craftsmen.
After our bells are removed from the pit and shaken out of the mold, they go through our tuning process to bring each of the five most prominent partials in agreement with each other. This is achieved by removing certain amounts of metal from the interior of each bell on a lathe or vertical boring machine.
Multiple partial tones are produced when a bell is struck. The five most prominent of which help to establish a bell’s overall timbre and are tuned to extremely close tolerances in order to ensure that each bell sounds according to client specifications. These partial tones are so named:
- HUM: the lowest partial.
- PRIME or FUNDAMENTAL: the main partial or root partial from which all of the other partials musically relate; is one octave above the HUM
- TIERCE or MINOR THIRD: this partial gives bells a melancholy sound
- QUINT or PERFECT FIFTH: above the PRIME
- NOMINAL: partial that is one octave above the PRIME. Naming note.
Bell partials are measured according to both their pitch in frequency (Hz) as well as their interval between cents or the equal temperament between one pitch to the next. These different partial tones and the timbre of each bell are created by many factors. Principally these being: alloy and metallurgical processing of the bronze prior to casting, profile design (the actual shape of the bell), casting conditions, mold material, pouring temperature and finally tuning.

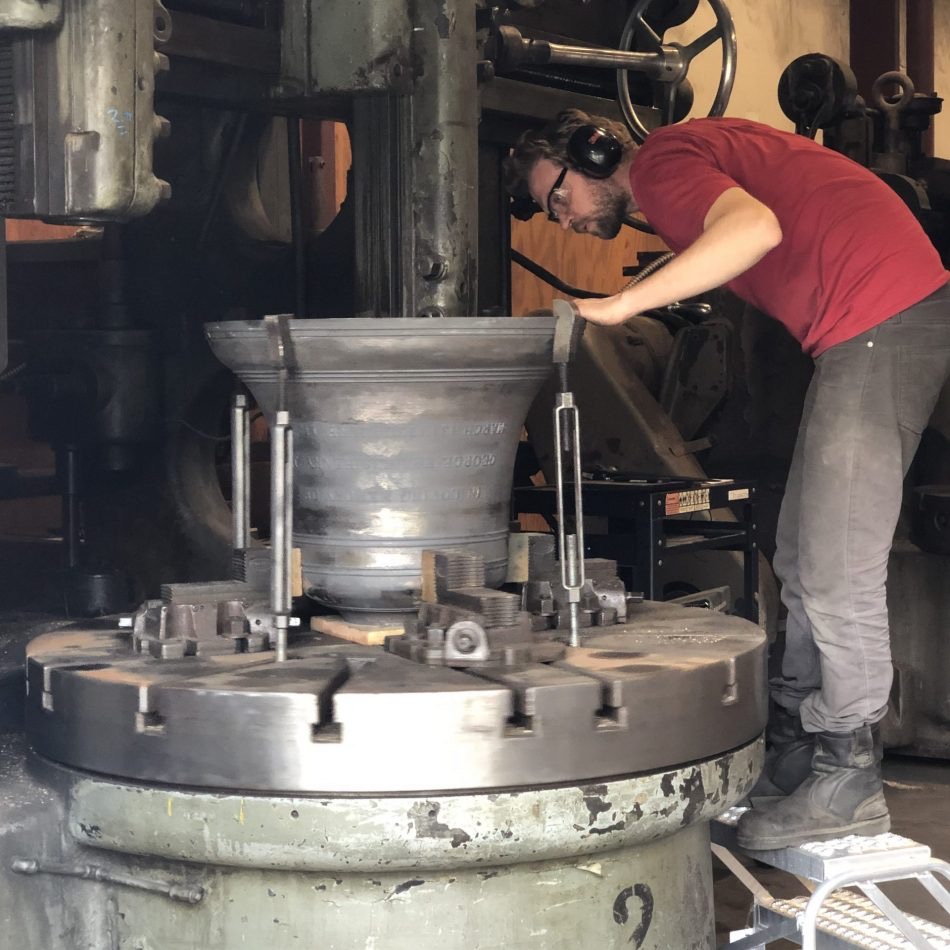
The Tuning Process
Standard practice calls for casting a bell thicker than what is required in order to work with a tuning reserve along the interior of the bell. This additional metal initially raises the overall pitch of the bell and is the reason why bells do not sound very good when removed from the mold. An initial tonal analysis is taken from the bell in the ‘as cast’ state in order to establish a method for tuning. Rarely, bell partials are in such proportion that they require little to no tuning in order to bring it to a suitable state. These bells are referred to as maiden bells.
Bells are then installed into lathes, both horizontal and vertical depending on size, in order to cut metal out of the interior of the bell to bring each partial tone in agreement with the other. This is a laborious and tedious task that takes great care in order to accomplish. This is also the moment when a bell’s sound is finalized and will be the sound that is produced over centuries of use. Once tuned, bells never should fall ‘out of tune’ with proper maintenance and care. The tuning process for bells could be compared to something like diamond cutting; only removing what is essential in order to bring out the sweet brilliance and clarity of the material. If too much metal is removed from a bell, the overall partials will become flat and hollow, rendering the bell unsuitable for use. The bell then must be broken up and tossed back into the furnace to be remade.
Musically speaking, all pitches and frequencies regard the international standard of A=440Hz. Industry standards for tuning tolerances are +/- 4 cents for carillon tuned bells and +/- 12-25 cents for church bells that are to be used for other purposes than playing structured music.